Marzocchi ALM Gear Motors
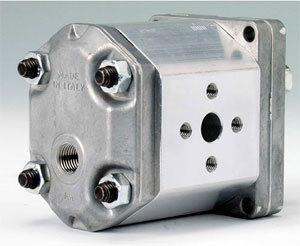
Marzocchi Gear Pump Technical Information
Marzocchi ALM Gear Motors
Marzocchi Group ALM1 | Uni-directional motors | Bi-directional motors |
Displacement | From 2.8 to 13.8 cc/rev | From 2.8 to 11 cc/rev |
Max. Continuous Inlet Pressure PI | 250 bar | 250 bar |
Max. Continuous Backpressure PC | 6 bar | 240 bar |
Max. Peak Inlet Pressure PP | 290 bar | 270 bar |
Max. Speed | 6000 rpm | 5000 rpm |
Max. Drain Line Pressure | —- | 6 bar |
Group ALM2 | Uni-directional motors | Bi-directional motors |
Displacement | From 4.5 to 35.2 cc/rev | From 4.5 to 28.2 cc/rev |
Max. Continuous Inlet Pressure PI | 250 bar | 250 bar |
Max. Continuous Backpressure PC | 6 bar | 240 bar |
Max. Peak Inlet Pressure PP | 290 bar | 270 bar |
Max. Speed | 4000 rpm | 4000 rpm |
Max. Drain Line Pressure | —- | 6 bar |
Marzocchi Group ALM3 | Uni-directional motors | Bi-directional motors |
Displacement | From 20 to 87 cc/rev | From 22 to 87 cc/rev |
Max. Continuous Inlet Pressure PI | 230 bar | 230 bar |
Max. Continuous Backpressure PC | 6 bar | 220 bar |
Max. Peak Inlet Pressure PP | 270 bar | 250 bar |
Max. Speed | 3500 rpm | 2500 rpm |
Max. Drain Line Pressure | —- | 6 bar |
Basic Marzocchi Design Information

External gear pumps are the most popular pumps used in modern hydraulic systems. They feature versatility, strength and long useful life. Their simple construction ensures limited purchase costs and servicing.
Thanks to these basic concepts, together with ever-improving product design and features, research -based on many years of experience – accuracy in material selection, production process followed in great detail and tests on mass-produced parts, our gear pumps have reached top quality standards.For this reason, our products can work under heavy operating conditions and transmit high hydraulic power. Furthermore, Marzocchi pumps feature good hydraulic, mechanical and volumetric efficiency, low noise level and, last but not least, compact dimensions and low weight/power ratio.
A gear pump usually consists of a gear pair supported by two aluminum bushes for groups 0.25, 0.5 and 1P, or bushes with plain bearings coated with antifriction material for groups 1, 2, 3 and 4, a body, a securing flange and a cover. Shaft of the driving gear projecting beyond the flange mounts a twin-lip seal ring (the inner lip being a seal, the outer lip being a dust seal) for groups 0.25, 0.5 and 1P, or two opposed single-lip seal rings (the outer being a dust seal) for groups 1, 2, 3 and 4.
Pump body, flange and cover are made of special hi-resistant aluminum alloys for minimized deformation even when subject to high pressure, be it continuous or intermittent or peak pressure. The body is profiled by means of extrusion, whereas flange and cover are obtained by means of die-casting (even gravity die-casting for some models).
Gears are made of special steel. Their manufacturing process includes case-hardening and quench hardening. Then gears are ground and fine finished so to have a high degree of surface finishing. Proper tooth profile design and geometric proportions ensure low pulsation levels and low noise levels during pump operation. Bushes are made of special low-friction and hi-resistant aluminum alloy and manufactured from die-casting.
Special compensation zones onto flange and cover, insulated by special seals with anti-extrusion rings, allow fully free axial and radial movement to the bushes, which is proportional to pump operating pressure. In this way, internal dripping is dramatically reduced, thus ensuring very good pump performance (both in terms of volume and in general) and proper lubrication of pump moving parts.
We offer the above from the following Brands
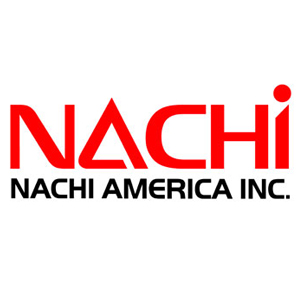
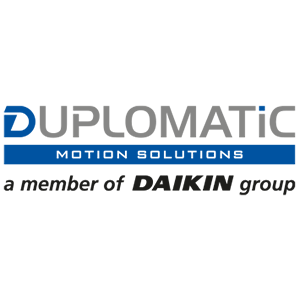
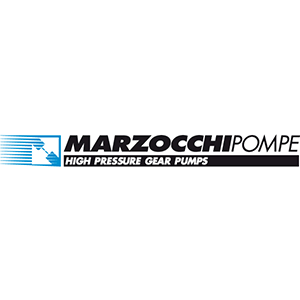
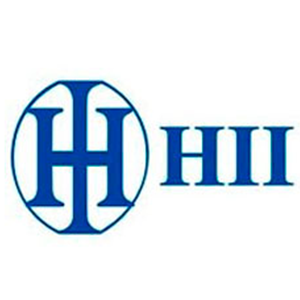
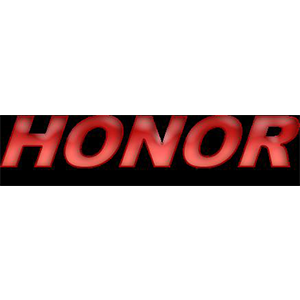
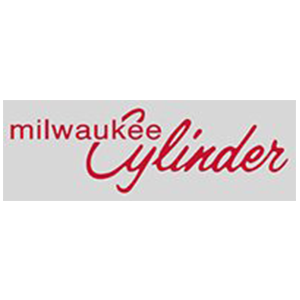

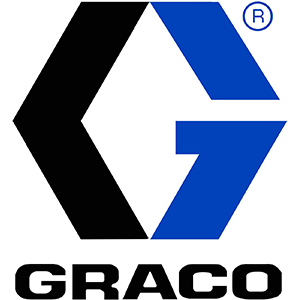